The DTF process is as simple as its name implies - print on film and then transfer directly to the fabric. The most significant factor that makes this process worth using by more people is that people are free to choose almost any fabric. Whether it is polyester fiber, cotton fiber, silk or synthetic fibers such as rayon or terrycot,
DTF printing process will certainly play a magical role in them. DTF is a process that uses a hot pressing mechanism to transfer printed matter to fabric or other substrates. Different from the DTG method only applicable to cotton fabrics, the printer DTF method is applicable to cotton and polyester blended fabrics.
DTF printing can maximize your personalized value. For a long time, the pursuit of trend and personality has become a way for many people to realize their self-worth, which is perfectly reflected in life. Now DTF printing enables any recognized value to be reflected in your belongings.
1.
T-shirt. One of the most common products for DTF printing is T-shirts. The demand for T-shirts has been high and can be used for a variety of purposes, from schools to sports to other organizations.
2.
A pocket on a Hoodie or shirt. Printing on a T-shirt may be easy, but when you want to print on a T-shirt pocket or front pocket of a hoodie, DTF printing can help you print in these difficult areas of your clothes.
3.
Hat. From baseball caps, truck driver hats to other styles of hats, it is difficult to print them without damaging them. DTF printing technology can print logos and designs on hats with challenging shapes.
4.
Print labels. Many clothing companies choose to print labels inside their clothing products, and DTF printing is a way to achieve this.
5.
Shorts / pants. Unlike T-shirts and other clothing, DTF printing allows you to print logos and designs on shorts or pants.
6.
Bag. DTF can be printed on handbags, waist bags, wallets, Drawstring Bags and many other types of bags.
7.
Flag / banner. DTF printing need not be limited to wearable fabrics. Other items, such as flags, banners and tablecloths, can be printed on them for events and expositions.
8.
KUZ. Another popular non clothing print is koozies, which keeps canned and bottled drinks cold. Any other fabric items. There are no restrictions on the creation of DTF printing in clothing.
Prerequisites for DTF printing-
The requirement of DTF printing does not require users to make a lot of investment. No matter who is currently engaged in one of the above digital textile printing processes and wants to expand DTF printing as a business, or who wants to get involved in digital textile printing from DTF, they must invest in the following aspects——
Direct to film printers - these printers are often referred to as DTF improved printers. Most of these printers are basic 6-color ink tank printers, such as Epson L800, l805, l1800, etc. The reason for choosing this series of printers is that they can use six colors. This facilitates operation because CMYK DTF ink can enter the standard CMYK tank, while the LC and LM tanks of the printer can be filled with white DTF ink. In addition, the roller used to slide the page is also removed to prevent "lining" on the white layer printed on DTF film.
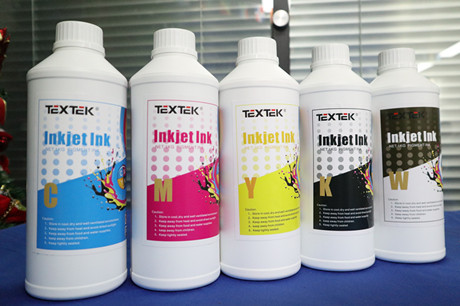
Film – PET film is used in DTF printing process. These films are different from those used for screen printing. Their thickness is about 0.75 mm, which has better transmission characteristics. In market language, these are often referred to as DTF transfer membranes. DTF films are available in two forms: cutting sheet (which can be used for small-scale use) and roll (used with commercial devices). Another classification of PET films is based on the type of peel after transfer. Depending on the temperature, the film can be a hot peel film or a cold peel film.
Software - software is an important part of the process. The software has a great influence on the printing characteristics of ink, color performance and the final printing performance on the fabric after transfer printing. For DTF, a special RIP software that can handle CMYK and white is needed. Color analysis, ink volume, droplet size and other factors affecting the optimized printing results are controlled by DTF printing software.
Hot melt adhesive powder – DTF printing powder is white and acts as a bonding material to bond the colored pigments in the printed matter to the fibers in the fabric. There are different grades of DTF hot melt powder, in microns. The appropriate grade shall be selected according to the requirements.
DTF printing inks - these are specially designed pigment inks in cyan, magenta, yellow, black and white. White ink is a special component. It prints white background color and color pattern on printed matter.
Automatic powder shaker - automatic powder shakers are used in commercial DTF units to apply powder evenly and remove excess powder.
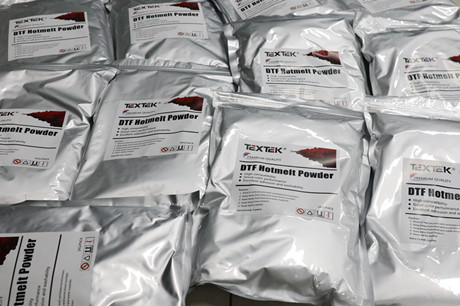
Curing furnace - the curing furnace is basically a small industrial furnace for melting hot-melt powder coated on the transfer film. Alternatively, a hot press can be used for this operation, but it should be used in contactless mode.
Hot press - hot press is mainly used to transfer images printed on film to fabrics. It can also be used to heat hot-melt powder on DTF film. The procedure described in detail below describes how to do this in.
Direct to film printing (basic steps) –
Step 1 - print on film
Insert PET film instead of plain paper into the printer tray. First, print the whole image in white on PET film. Then, the desired image is printed on the white image layer using the appropriate color settings in the printer. It is important to remember that printing on film must be a mirror image of the actual image that needs to appear on the fabric.
Step 2 - powder
This step is to apply hot-melt powder to the film with printed image. When the printed matter is wet, the powder is evenly applied, and the excess powder needs to be carefully removed. It is important to ensure that the powder is evenly distributed on the printed surface of the film. A very common way to ensure this is to keep the film on its short side so that its long side is parallel to the floor (transverse direction), and pour the film in the middle of the film from top to bottom to form a pile about 1 inch thick in the center from top to bottom. Pick up the film and powder together and gently bend it inward to form a slight U-shape with the concave side facing itself. Now gently shake the film from left to right to spread the powder slowly and evenly on the surface of the film. Alternatively, an automatic vibrating screen that can be used in commercial settings can also be used.
3. Molten powder
In this step, the powder is melted as shown in the name. This can be achieved in many ways. The most common method is to heat the film with printed image and powder in the curing furnace. If the curing oven is not available, place the film in the hot press so that the top of the hot press is very close to the film, but do not touch it. There should be a gap of about 4 to 7 mm between the film and the hot pressed top plate. A wire can be used to fix the top of the pressure so that it does not completely close the film and leave the necessary clearance. For best results, it is strongly recommended to follow the manufacturer's powder smelting specifications. Depending on the powder and equipment, the heating time is generally 2 to 5 minutes and the temperature is about 160 to 170 degrees Celsius.
4. Preloading
This step includes preloading the fabric before the film transmits the image. The fabric is held in a hot press and pressurized under heat for about 2 to 5 seconds. This is done to flatten the fabric and ensure that the fabric is dewatered. Preloading helps to transfer the image from the film to the fabric correctly.
Step 5 - transfer
This is the core of DTF printing process. The PET film with image and molten powder is placed on the pre pressed fabric in a hot press, so that there is a strong adhesion between the film and the fabric. This process is also known as "curing". Cure in the temperature range of 160 to 170 degrees Celsius, about 15 to 20 degrees Celsius. The film is now firmly attached to the fabric.
Step 6 - cold stripping
It is important that the fabric and the film now attached to the fabric must be cooled to room temperature before the film is torn off. Because the property of hot melt adhesive is similar to amide, when it cools, it acts as an adhesive to firmly bond the colored pigment in the ink with the fiber of the fabric. After the film cools, it must be stripped from the fabric to leave the required ink pattern on the fabric.
Step 7 - back pressure
This is an optional step, but it is strongly recommended to use it for best results and high performance parameters such as washing fastness and rubbing fastness. In this step, the final fabric with transfer design is pressed in a hot press for about 10 to 15 seconds.
Some Details Of DTF Printer
DTF printing is more versatile than other printing technologies. DTF can be printed on various fabrics, including cotton, nylon, rayon, polyester, leather, silk, etc.
DTF printing has revolutionized the textile industry and updated textile creation for the digital age. The process is simple: digital artwork is made, printed on film, and then transferred to fabric.
More advantages of DTF printing:
It's easy to learn
No pretreatment of the fabric is required
The ink used in this process is reduced by about 75%
Better print quality
Compatible with multiple materials
Unparalleled quality and high productivity
Requires less space than other technologies
The DTF process enables creators to start working faster than DTG or screen printing technology.
Thus, the easy DTF four step process makes the fabric feel softer and provides higher washing resistance:
Step 1: insert the PET film into the printer tray and print.
Step 2: apply the hot-melt powder on the film together with the printed image.
Step 3: melt the powder.
4. Pre press the cloth.
Designing DTF printing patterns is as simple as designing on paper: the design is sent from the computer to the DTF machine, and the rest is completed by the printer. Although DTF printers look different from traditional paper printers, their functions are very similar to other inkjet printers.
In contrast, screen printing involves dozens of steps, which means that it is usually only suitable for the simplest design or the cost-effectiveness of a large number of projects.
Although screen printing still occupies a place in the garment industry, DTF printing is more affordable for small enterprises or textile institutions who want to place small orders.
DTG:
It requires pretreatment: for DTG, the process starts with the pretreatment of clothing. This step is necessary before printing, because we will work directly on the fabric, which will fix the ink well and avoid transfer through the fabric. In addition, we need to heat the clothes before printing to activate this process.
Print directly to clothes: with DTG, you can print directly to clothes, so the printing process can be shorter than DTF without transfer.
Use white ink: we can choose to use a white mask as the base to ensure that the ink does not mix with the color of the medium, although this is not always necessary (e.g. on a white base). We can also reduce the use of such masks and only use white masks in some places.
Cotton print: this print can only be printed on cotton clothes.
Last ironing: in order to repair the ink, we must get the clothes ready for the last ironing.
DTF:
No preprocessing: in DTF printing, because it is pre printed on the film and needs to be transferred, there is no need to preprocess the fabric.
Print on film: in DTF, we print on film, and then the design must be transferred to the fabric. This makes the process slightly longer than DTG.
Rubber powder: this kind of printing requires the use of rubber powder, which is used after printing ink on film. On printers created specifically for DTF, this step is included in the printer itself, so any manual steps can be avoided.
Use white ink: in this case, it is necessary to use a layer of white ink and place it on the top of the color layer. This is the basic color transferred to the fabric and used as the main color of the design.
Any type of fabric: one of the advantages of DTF is that it allows you to use any type of fabric, not just cotton.
Transfer from film to fabric: the last step is to transfer the printing film to the fabric with a press.
So what factors should we consider when deciding which print to choose?
Materials we print out: as mentioned above, DTG can only be printed on cotton, while DTF can be printed on many other materials.
Production capacity: at present, DTG machines are more versatile and can produce products larger and faster than DTF. Therefore, it is very important to clarify the production demand of each enterprise.
Results: the final results of the two prints were completely different. In DTG, painting and ink are combined with the fabric to make it feel rougher, just like the base itself. In DTF, fixing powder makes it feel more like plastic, brighter and less combined with fabric. However, it also gives people a feeling of higher color quality, because they are pure, so the primary color will not intervene.
Use of white: in essence, both technologies need a lot of white ink to print, but by using good RIP software, the white layer applied in DTG can be controlled according to the background color, so as to greatly reduce the cost.
The basic concept of DTF is to print CMYK first, and then print white on it. Always mirror your image first!
Most of you will print on standard A3 and A4 paper. Use every inch of space as much as possible to save time and material costs. We call it Gang cover. One advantage of GC is that it allows multiple images to be uploaded simultaneously for printing. The person who ordered the plastisol transfer already knows this. The two most common platens I use are 10 x 12 (A2) and 16 x 20 (A3). I put the sheets at the top of the middle as a reference and measure how much space there is at the side and bottom, because the sheets will be smaller than your platen. I use tape to fix the paper in at least two corners to prevent the paper from shifting during printing.
Using GC for DTF is very similar to using DTG. The only difference is that you are reversing the CMYK / white process and mirroring your image.
If you have black in your picture, click black clothes. This will prevent the GC from printing black unnecessarily.
For all other colors, including white, use (dark).
After choosing the right color, you need to adjust your color and whiteness. Personally, I use secondary color, primary white. I set the ink density to zero. And make sure there is enough time (seconds) between passes. This is very important. I like to choose 30-60 seconds
Under white management, it is very important to check "off" before printing CMYK pass. This will allow your color layer to fall first.
When the color transfer is complete, return to white management and click open. Make sure there is a sufficient number of seconds in "pause between passes (seconds)", otherwise the printer will print another CMYK pass immediately after the white pass. You don't want that! Therefore, you must manually press the Cancel button on the printer before the printer can perform this operation.
Unfortunately, garment creator is not designed for DTF, so you need to turn white on and off every time you print.
Powder should not be applied to the printer platen. It needs to be used away from the printer. If the printer "sucks" the rubber powder into the air inlet fan through the electronic equipment near the rear of the machine, painting near the printer will increase the risk of damage to the printer. Damage to the printer due to improper use may not be covered by the warranty.
When using DTF products, please wear personal protective equipment (glasses, masks and gloves). Fumes from solidified powders can be harmful.
DTF (direct coating) products are applicable to almost all types of fabrics, including 100% polyester fiber, with good quality effect!
The designed fabric or printed shirt has good washing characteristics.
This fabric feels very light.
DTF VS DTG
If you want to know the price and maintenance, they are similar. In fact, you just need to shake the ink cartridge and print it, then use the foam cotton swab to clean the station / print head.
If the transfer is correct, gently powdered and at the appropriate ink level, the result will be very soft and smooth as well. You basically add plastic to a layer of wet ink on the back. Then press the plastic into the shirt as an adhesive. So now, unlike the DTG method, the ink will adhere to the top, but there is a layer of plastic under it.
However, the larger the print, the more eye-catching it is.
In short, DTG seems to be more practical, but obviously DTF is the simplest.
If you are looking for a reputable way to start a business and want to maintain high-quality products, you will not only use DTF printing.
It is an excellent complement to DTG / screen printing. However, you can use it to achieve this goal, which is up to you. But in this regard, comparing them according to the ease and cost of maintenance is not the only problem you need to consider.
The best way for anyone to decide which method to use is to get a sample of each method! Compare them and randomly ask your friends which one they prefer and which one they are willing to pay for.
We hope this information will simplify your decision and clarify your views on the new trend of DTF printing.
Have you tried this at home, or have you printed DTF? Write to us!

For DTG, you have a printing that can penetrate most of the fabric, but the ink layer is very thin and flexible. It will be washed away after pretreatment.
In screen printing, you push the ink into the fabric and leave a small deposit on it. It is also a very thin layer of flexible ink, but it can be very thick or very thin depending on what you do, which depends on yourself. I thinned my hair as thin as I could, and the result was good.
DTF uses the same aspect. If it is just ink, like the above two methods, it will be equally soft. However, you basically add plastic to a layer of wet ink on the back. Then press the plastic into the shirt as an adhesive. So now, the ink no longer adheres like the other two methods, but has a layer of plastic under it.
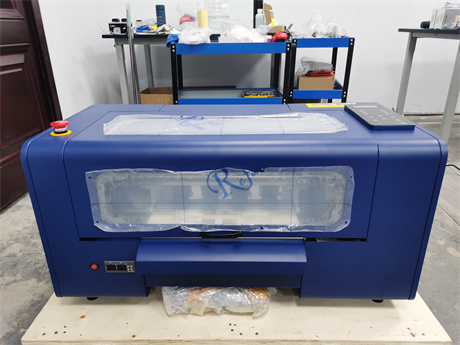
At present, there is no way to bypass this plastic, you can feel it. How to use this will have a huge impact.
In short, screen printing is the cheapest, DTG is the most common, and DTF is the simplest. The quality of each product reflects this. Some people will like it, some people will hate it, some people will indulge in it and decide to use other things, just like all the new things in this market. In the past five years, I have seen at least four new "wow" products appear and disappear.
If you are looking for a reputable way to start a business and want to maintain product quality, you will not only use DTF transfer. It is an excellent complement to DTG / screen printing. However, you can use it to achieve this goal, which is up to you. But in this regard, comparing them according to the ease and cost of maintenance is not the only problem you need to consider.
For anyone, the best way to decide which method to use is to obtain DTG samples, DTF samples and screen printing material samples. Compare them all, blindly ask your friends which one they like and which one they will pay for, and then invest thousands of dollars in something that may eventually burst in your eyes. In the final analysis, only you are responsible for what your money is spent on.
We are a manufacturer specializing in the R & D, production, sales and service of fabric printing machines. We provide textek large DTF printer, A3 DTF printer, sublimation fabric printer, direct textile printer and related consumables, such as DTF ink, PET film, powder, etc.
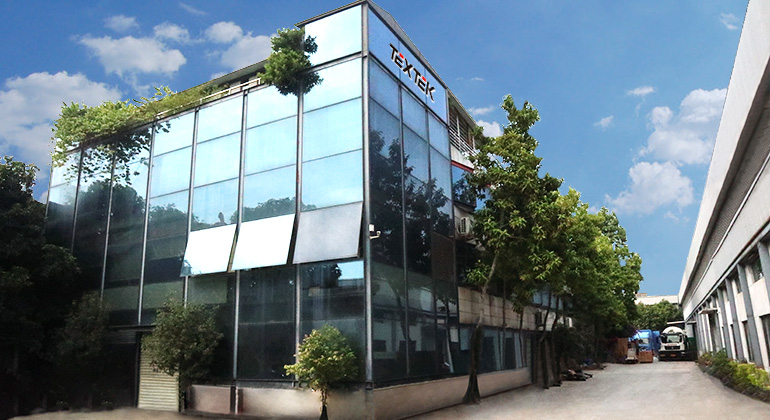
Through cooperation with world-famous print head manufacturers and software suppliers, we integrate exquisite and practical technology into our fabric printers. For many years, textek printer factory has been providing customers with a variety of printing solutions with high-quality printers and competitive prices, and is committed to making it easier for customers to complete printing.
DTF printer factory has absorbed and gathered a group of high-quality professional and technical personnel and enterprising young management team. With our enthusiasm and professional knowledge of fabric printing, we focus on providing cost-effective 60cm DTF printers, A3 DTF printers, dye sublimation printers, direct fabric printers, etc.